Taiyo-sha (Gifu)
Solving the problem of a lack of manpower in the prepress process with the introduction of PTS
Reducing the number of man-hours required by 80% – from 5 operators to a 2-person system
15 February 2025 17:38 Company Report
Creating new value with the theme of âthe library of publishingâ – Taiyosha, a company that boasts an 82-year history in publishing and printing (Headquarters: 148-1 Kitagata, Kitagata-cho, Motosu-gun, Gifu Prefecture; President: Shigenori Omichi), introduced the Plate Transportation System (PTS) proposed by ECOSYS last October introduced the Plate Transportation System (PTS) proposed by ECOSREE, against a backdrop of a worsening shortage of labour. By automating the process from punching and plate bending of the five types of plates output from the two CTPs to the automatic sorting of the plates into the ten types of stackers, the number of times the workers touch the plates has been reduced by 80%. The company has succeeded in reducing the number of sta and the time required for the plate-making process, as well as eliminating plate-related problems.
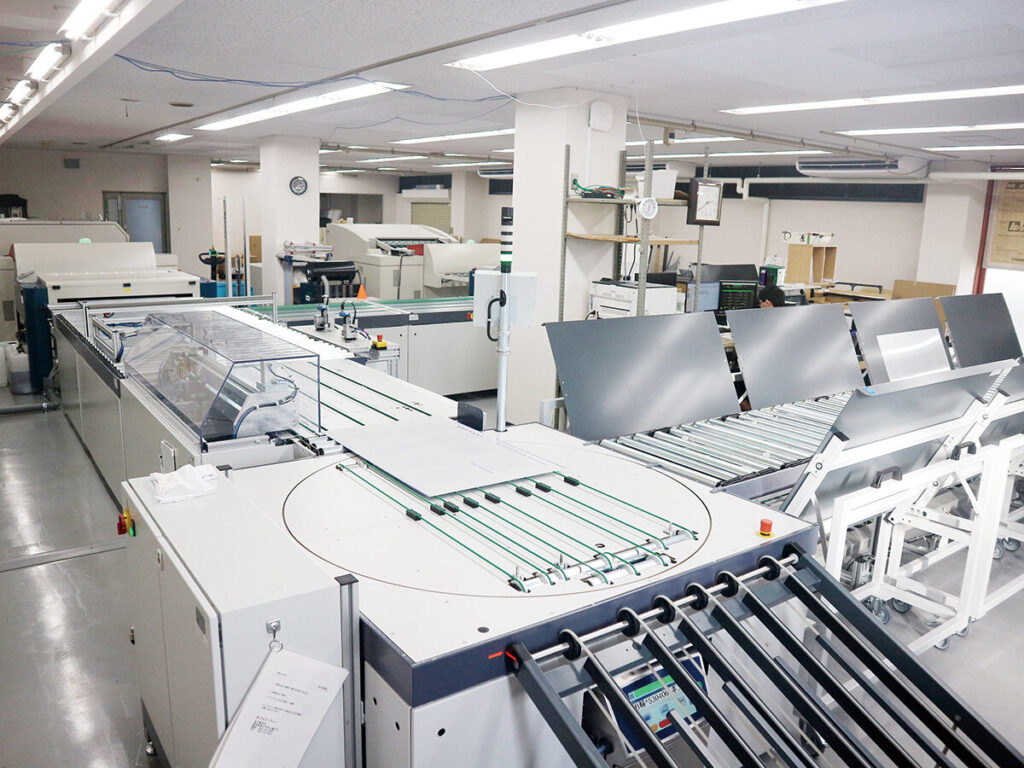
Publishing + four new businesses
Taiyo-sha was founded in 1921. It was a privately-run company that mainly worked with apparel-related companies, and then in 1943, when the war was becoming increasingly fierce, it was established. Fortunately, the company was spared from the ravages of war, and it received many jobs, mainly telephone directory printing, not only from within the prefecture but also from Aichi and Shiga prefectures. It is a long-established printing company that achieved rapid growth in the post-war reconstruction period.
The turning point for the company was the introduction of an o set printing press in 1967. Based on the management strategy of âmaking a major shift towards a printing business specialising in the publishing fieldâ, the company introduced a vertical A-size o set printing press, which was not widely used in Japan at the time, at the same time as the completion of the Hokuto factory. Since then, the company has been known as âTaiyo-sha of publishingâ and as âa company that continues to make books with unwavering integrityâ.
The company is known for its educational materials, such as textbooks, reference books, company histories and dictionaries, and it is particularly well known for printing the so-called âred booksâ, which are past question collections for university entrance exams by university and faculty, published by Gakushu-sha. The company has a 45% share of this market, which accounts for around 23% of its total sales.
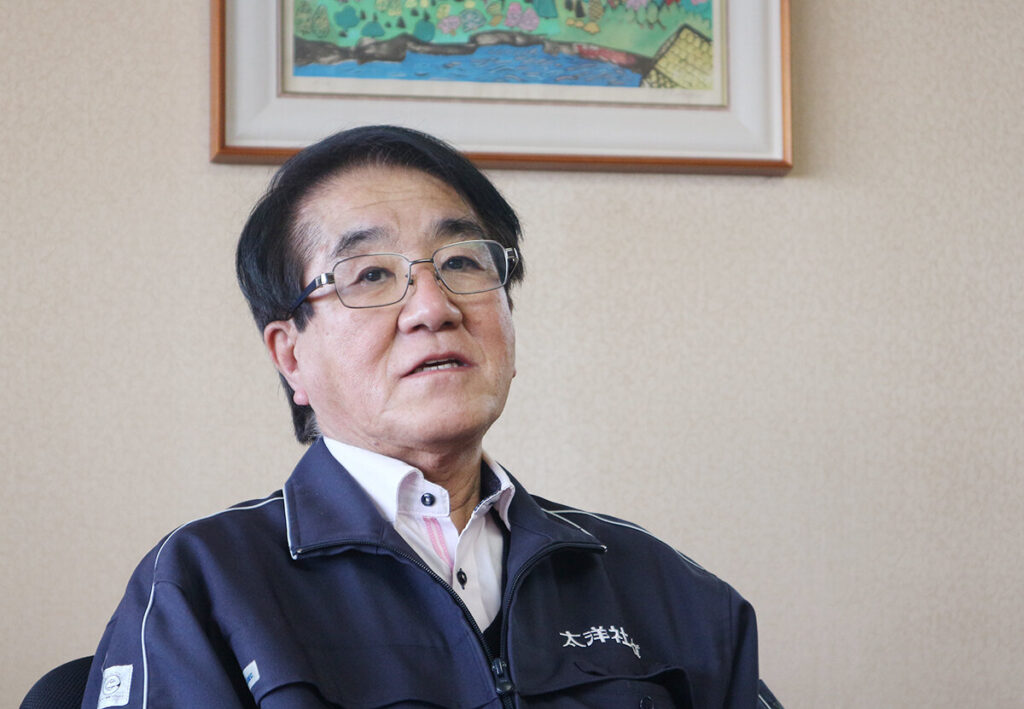
On the other hand, President Omichi, who is now in his ninth year in o ice, is growing increasingly concerned about the future of printing management, saying, âWe can’t continue to rely on printing alone.â Four years ago, he took the advice of a management consulting firm and launched two new businesses in addition to the printing business, bringing the total to four.
First, in the printing-related field, he established a planning and sales department and began a public relations and event support business for all 42 cities, towns and villages in Gifu Prefecture. The second new business is anniversary event projects for companies, schools, hospitals, etc.
On the other hand, in 2021 they started an agriculture business that is not related to printing. They grow shiitake mushrooms and kikurage mushrooms in Waracho, Gujo City, Gifu Prefecture. The other new business is the establishment of programming classes for elementary school students. Both of these are new businesses that are closely connected to the local community, and the company has started to diversify its management.
Automatic sorting into 10 different stackers
A special feature of the company is its integrated production system, which enables it to offer all processes from typesetting to plate production, printing, binding and logistics from a single source. For this reason, we are very confident that we will be able to meet delivery deadlines. On the other hand, the company was faced with an ageing workforce at all levels, so the recruitment of new staff was urgently needed. Hori Tomoyuki, General Manager of Prepress, recalls: âEspecially in the plate printing department, which had five employees, several people were about to retire. The plate printing process was separated from the printing site and almost half of the plate transportation, punching and bending work was done by hand, so we had to increase our staff. However, with the general labor shortage becoming more chronic, the plate printing process is not an easy job, so it was difficult to attract new talent.â
As a solution, we focused on automating the printing process. The project was initiated when Eco3, which uses workflow-related products, proposed the Plate Transportation System (PTS).
PTS is an automated solution that enables everything from plate bending to automatic distribution to stackers. Hori immediately visited an existing user in Tokyo and said he was âimpressed that there was no one thereâ. However, he noted that automating the process would be difficult as the company uses five different panel sizes. However, because it would significantly reduce human labor, optimize staffing, and eliminate the human-caused problems associated with the manual work of punching and bending plates, the prepress and print shop sites unanimously decided to adopt the technology.
Was there no room for comparison and consideration of automation systems from other manufacturers when making this decision? Shimizu Kazunari, Manager of the Prepress Division, explains: âAs Eco3 products dominate our CTP and workflow, we had almost no other options. Automated systems such as PTS are controlled by signals from the equipment, so the hurdles are high when mixing different manufacturers. In addition, it is difficult to determine the cause when problems occur. Eco3 has a reputation for always coming up with innovative proposals, such as PDF workflow, cloud computing and subscription services. One of the things they suggested was a PTS tailored to our business, so we wanted to work with them.â
It was actually installed in October last year. The launch work was carried out over two three-day weekends. The process of the implemented PTS is as follows:
First, the plates printed by the two CTP machines are brought together on a single transport rail. The QR code can be used to read whether the plate has been punched and bent. After each process, the order information is printed on the back of the plate using an inkjet printer. Finally, the panels are sorted into 10 different stackers either by printing machine or by front and back.
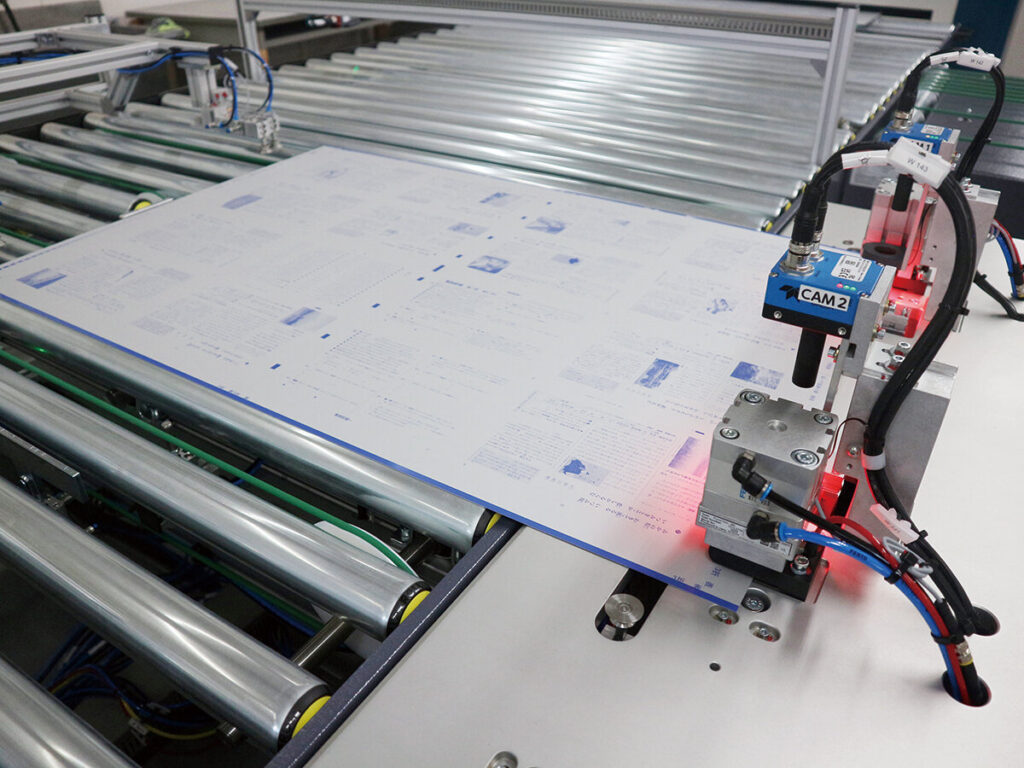
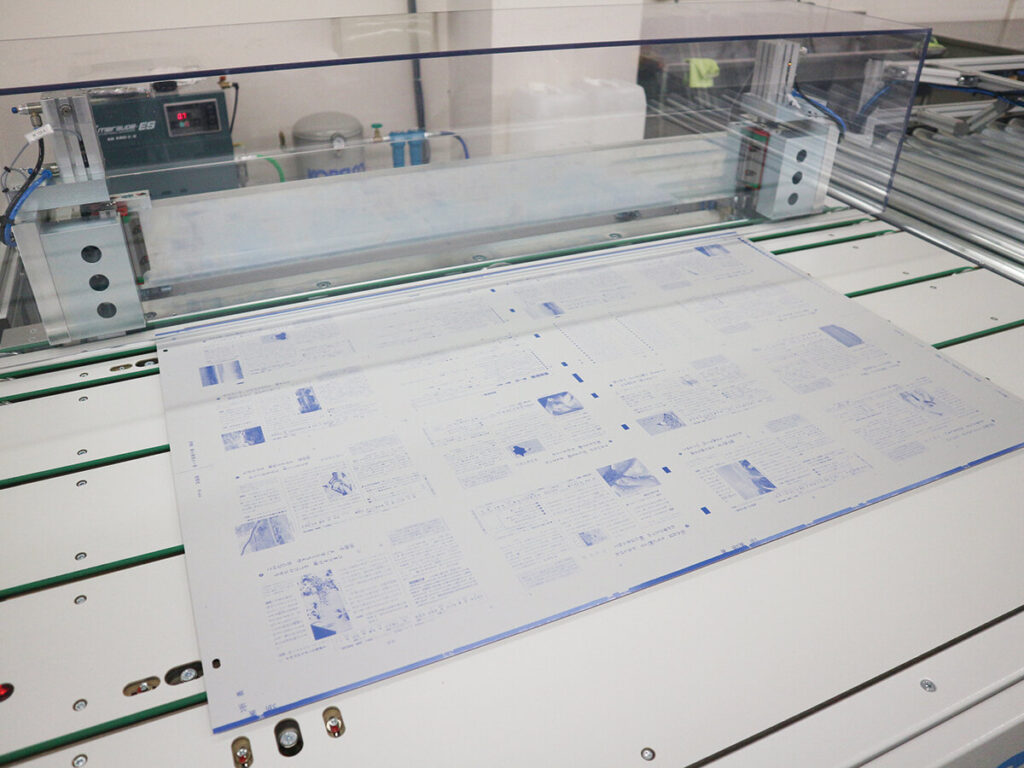
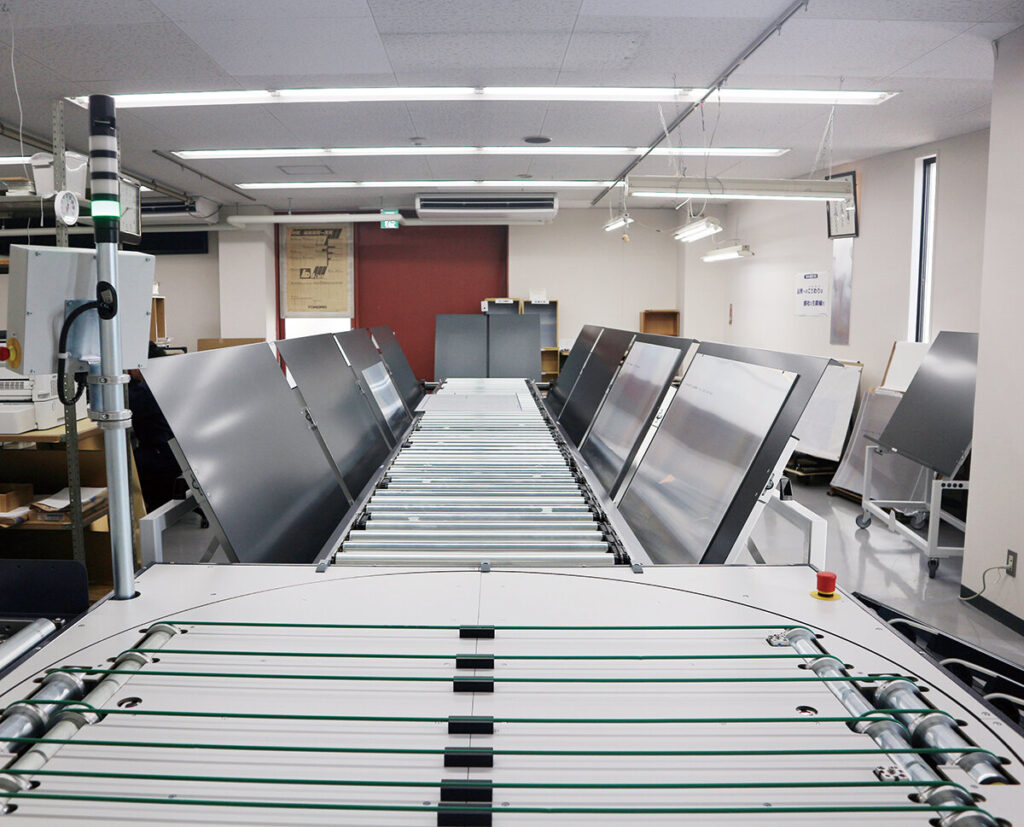
âWe have four web o set presses and four sheet-fed presses, and we also sometimes outsource work to other companies, so ten types of stacker are not enough. We have solved this problem with flexible operation, partly due to space constraintsâ (Mr Shimizu, Manager).
381 hours saved per year just from bending plates
The company has achieved automation by incorporating all of the following into the PTS line: special punches that could not be handled by the CTP inner punch and had to be handled manually, plate sorting that was complicated due to the large number and variety of printing presses, and handwriting job information on the back of the plates. As a result, the number of staff in the printing department was reduced from five to two. In addition, the number of times workers touched plates when sorting and transporting them was reduced by 80%, which also succeeded in preventing handling problems that depend on people (see figure). Looking at this in terms of work time, first, in the plate bending process, plates are carried to the bender in the plate room and bent, for a total of 45,800 plates per year. Assuming that this takes 30 seconds per bend, this translates into a reduction in work time of 381 hours per year. In addition, punching work involves transporting plates to the punch machine in the plate room and punching 10,200 plates per year. Assuming each punch takes 30 seconds, this will reduce work time by 85 hours per year. Furthermore, when it comes to the task of writing job information, assuming that the handwritten work of 100,000 copies per year takes 20 seconds each time, this will be reduced to zero, resulting in a reduction of 555 hours of work time. Yamazaki Shota, deputy manager of the Prepress Division, explains the effects of the system, saying, “Until now, even if we were able to finish printing plates within working hours, the punching and plate bending work sometimes meant overtime or had to be carried over to the next day. Now, we can complete everything within working hours, and there are no more problems such as scratches. We’ve achieved the desired effects of the introduction by reducing the number of people, cutting working hours, and eliminating plate problems.” With an automated system like this, support is extremely important when problems occur. How will Eco3 respond? “Of course, there were some small initial issues, but communicating with the PTS manufacturer through Eco3 Japan was stress-free and we received quick feedback. Program changes were handled remotely directly from Germany, so we didn’t feel any particular time lag,” said Shimizu.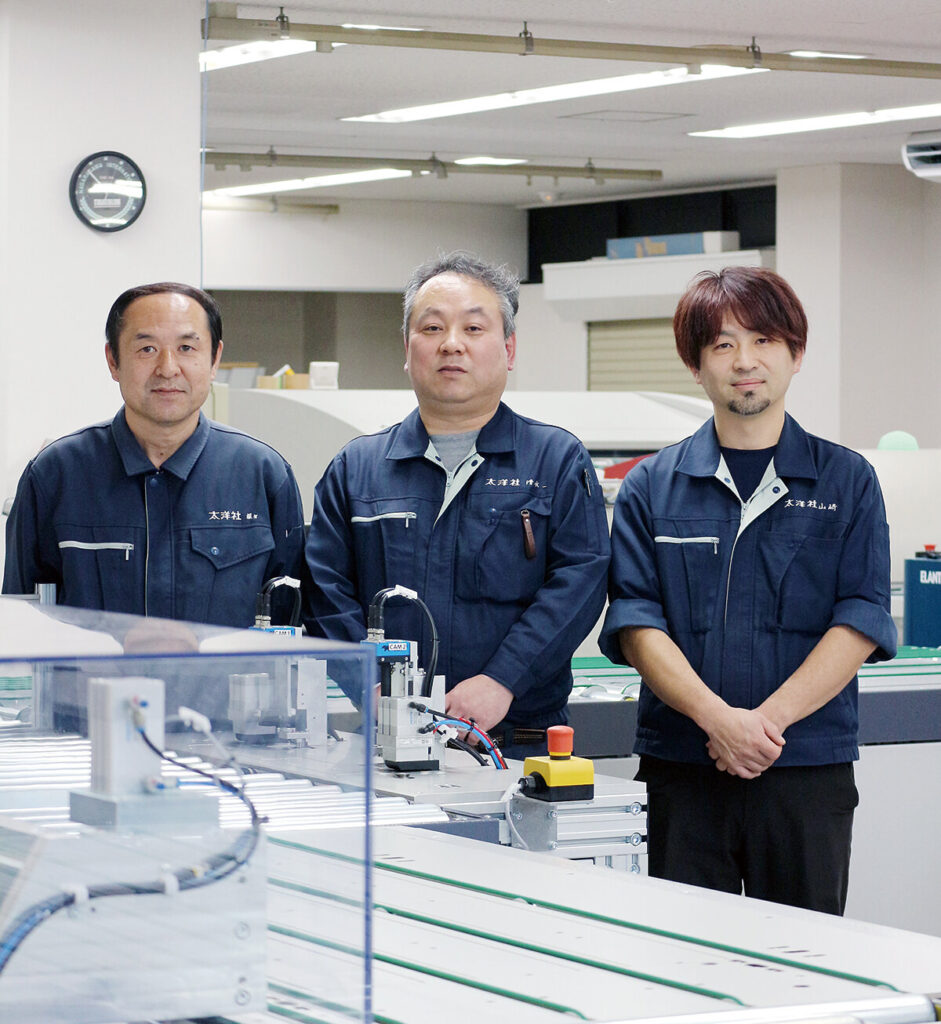